Specialist Suggestions on What is Porosity in Welding and Just How to Resolve It
Wiki Article
Porosity in Welding: Identifying Common Issues and Implementing Best Practices for Prevention
Porosity in welding is a prevalent issue that frequently goes undetected up until it causes significant troubles with the stability of welds. In this discussion, we will certainly check out the key variables adding to porosity formation, analyze its harmful effects on weld efficiency, and talk about the best methods that can be adopted to decrease porosity incident in welding processes.Usual Root Causes Of Porosity
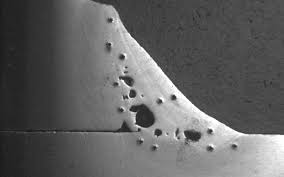
One more frequent perpetrator behind porosity is the presence of pollutants on the surface of the base metal, such as oil, oil, or rust. When these pollutants are not effectively eliminated prior to welding, they can vaporize and end up being entraped in the weld, triggering issues. Using filthy or damp filler materials can introduce contaminations into the weld, contributing to porosity problems. To minimize these common root causes of porosity, complete cleaning of base metals, correct protecting gas choice, and adherence to ideal welding criteria are crucial practices in achieving premium, porosity-free welds.
Impact of Porosity on Weld Quality

The visibility of porosity in welding can significantly compromise the architectural honesty and mechanical residential or commercial properties of welded joints. Porosity produces spaces within the weld metal, compromising its general stamina and load-bearing capability. These voids serve as tension concentration points, making the weld more susceptible to cracking and failure under used lots. In addition, porosity can minimize the weld's resistance to rust and other environmental factors, further lessening its long life and efficiency.
Among the main consequences of porosity is a decline in the weld's ductility and sturdiness. Welds with high porosity levels tend to show reduced impact toughness and minimized ability to flaw plastically prior to fracturing. This can be particularly worrying in applications where the welded components undergo dynamic or cyclic loading problems. Porosity can impede the weld's capacity to effectively transfer forces, leading to premature weld failure and prospective safety dangers in crucial frameworks. What is Porosity.
Finest Practices for Porosity Avoidance
To boost the structural honesty and top quality of welded joints, what certain actions can be implemented to reduce the incident of porosity throughout the welding process? Using the correct welding technique for the details material being welded, such as adjusting the welding angle and weapon placement, can better protect against porosity. Routine assessment of welds and immediate remediation of any kind of problems identified during the welding procedure are necessary methods to prevent porosity and generate top notch welds.Value of Proper Welding Strategies
Applying appropriate welding techniques is extremely important in making sure the structural honesty and high quality of welded joints, building on the foundation of my link reliable porosity prevention measures. Welding strategies directly influence the general toughness and toughness of the welded framework. One essential facet of proper welding strategies is preserving the proper warm input. Too much warm can lead to boosted porosity due to the entrapment of gases in the weld swimming pool. Conversely, inadequate heat may cause incomplete blend, creating prospective powerlessness in the joint. Furthermore, making use of the suitable welding criteria, such as voltage, current, and take a trip rate, is essential for attaining sound welds with very little porosity.In addition, the selection of welding process, whether it be MIG, TIG, or stick welding, ought to straighten with the details requirements of the project to make see it here sure optimum outcomes. Proper cleaning and preparation of the base metal, in addition to choosing the appropriate filler product, are additionally essential components of skilled welding methods. By sticking to these finest methods, welders can lessen the threat of porosity development and generate high-grade, structurally audio welds.

Evaluating and Quality Assurance Actions
Examining treatments are necessary to find and stop porosity in welding, making sure the strength and sturdiness of the last product. Non-destructive testing approaches such as ultrasonic testing, radiographic testing, and aesthetic examination are generally utilized to determine potential defects like porosity.Carrying out pre-weld and post-weld inspections is additionally important in maintaining top quality control requirements. Pre-weld evaluations entail confirming the materials, tools settings, and sanitation of the workplace to stop contamination. Post-weld assessments, on the other hand, analyze the final weld for any type of problems, consisting of porosity, and verify that it satisfies specified requirements. Carrying out a detailed quality assurance plan that consists of extensive screening procedures and examinations is critical to minimizing porosity issues and making sure the total high quality of bonded joints.
Final Thought
In verdict, porosity in welding can be an usual issue that impacts the quality of welds. By determining anonymous the typical reasons of porosity and implementing best practices for prevention, such as appropriate welding methods and screening procedures, welders can guarantee top quality and trusted welds. It is necessary to prioritize prevention techniques to lessen the event of porosity and keep the honesty of bonded frameworks.Report this wiki page